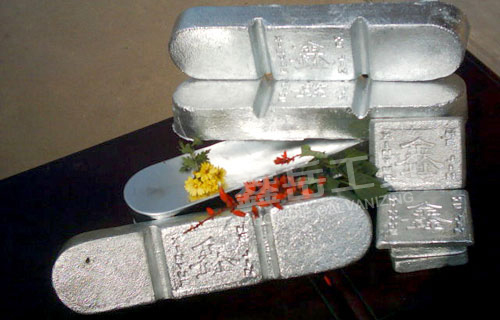
Design and Construct Hot Dip Galvanizing Plants both Domestically and Internationally
Add: Jinshan Bridge Zone, Xuzhou, Jiangsu, China
Mobile: 86-13805211808
Tel: 86-516-83168088
Email: xy-rjd@163.com
In the present years, with the popularization of continuous casting technology in the iron and steel enterprises, the proportion of the silicon-killed steel to total steel products is growing. Because the silicon element in steel product can speed up the reaction between zinc and iron, as a result coating color is changed and color difference is serious. The difficult problem in the technology is a real headache for quite a few hot galvanizing plants and is also an important and key research project. For this reason, Our company has developed Xinyue Brand special multi-component zinc-based alloy for hot galvanizing. It has successfully solved this technical difficult problem and decreased production cost considerably. Through summing up experience of many years and constant improving, the zinc-based alloy has been used in many hot galvanizing plants at home and abroad and played an important role.
Main Characteristics:
The special purpose of the Xinyue Brand multi-component zinc-based alloy is to eliminate color change and color difference. At the same time it can raise the fluidness of molten zinc, increase brightness and decrease production cost:
Eliminating color difference: the alloy makes coating layer surface smooth, bright and uniform color;
Reducing coating player thickness: the alloy can restrain the influence of silicon, reduce coating player thickness and control coating player thickness according to technical requirement;
Extending zinc pot life: the alloy can prohibit the corrosion of zinc pot by molten zinc effectively, and thus it can expand the service life of the zinc pot;
Reducing zinc ash and slag: the alloy can decrease the oxidation of zinc, restrain the reaction between zinc and iron, eliminate iron and reduce the growth and spallation of float layer and decrease the formation of ash and slag considerably.
Raising coating quality: after using the alloy, improved metallographic structure can make coating layer structure closer, adhesion stronger and coating surface brighter and more beautiful.
Increasing fluidness: After addition of the alloy into molten zinc, its fluidness increases by more than two times (under the same temperature). Because of good fluidness, the list edge and burr of workpiece from zinc pot are decreased, the product quality is guaranteed, pure zinc player thickness is reduced and the aim of zinc saving is realized;
Reducing galvanizing temperature: After addition of the alloy into molten zinc, the galvanizing temperature can decrease from 460-480℃ to 425-445℃ and a lot of energy can be saved. Zinc ash and zinc slag are reduced by over 20% and over 30% respectively. The corrosion of zinc pot and the formation amount of harmful gas and dust are decreased. The work environment is improved and the labor intensity of workers is decreased;
Increasing wettability: After addition of the alloy in to molten zinc, the wettability of molten zinc to workpiece increases effectively and galvanization-missing decreases.
Using Method
Prerequisite for using the alloy is that the existing operation process is not changed basically. The total consumption of the alloy is 1.2%-1.5% of molten zinc weight. The alloy should be added multiple times by batches during its first using period. From here on, the every addition level of the alloy is 1.5% of molten zinc weight each time.
After every addition of the alloy, it would be best if the liquid zinc could be in the standing condition for 30 min.
The cleaning agent of liquid zinc should be often used for eliminating slag, gas and iron to keep liquid zinc cleaned and decrease the iron content in it.
During first using the multi-component alloy, the additional amount of it is 0.5 % of liquid zinc and at the same time the temperature of molten zinc is at about 440℃. After the smelting of the alloy, according to zinc condition (if existing aluminum content in molten zinc is higher, it can be added by batches )and equal proportion, the multi-component alloy of the same weight is added into molten zinc before the proportion of the alloy in zinc pot reaches 1.5%.
After all the added alloy is melted, float slag treatment is carried out with cleaning agent (as thorough as possible) to eliminate the intrinsic gas and suspended material in molten zinc.
Eliminating aluminum: the aluminum content in molten zinc in some plants is higher and a part of it should be removed; otherwise there will be streak on the workpiece and even galvanization missing will form. Generally speaking ammonium chloride distribution method should be adopted before molten zinc surface is like a mirror and it can be kept for more than 30 min. without obvious change.
After the abovementioned the abovementioned treatment, the temperature is controlled at 440℃±5℃. The standing and heat-insulating time is 2~48 h, and the time should be as long as possible. (The standing and heat-insulating is very important because at this time the some elements in the alloy react with iron in molten zinc to eliminate iron. The alloying of whole pot of molten zinc needs about a week. During this period the production can be carried out normally and its effectiveness will become more and more obvious.) The sample of molten zinc is taken for chemical analysis and its iron content is not greater than 0.03%. If the content is greater than this value, the alloy should be added with repeating the above
Notes:
1. Do not add lead into molten zinc; otherwise after the alloy is added and the temperature is decreased, the small spangle on the workpiece can not be removed and soon the luster of it will be lost.
2. Do not add excessive amount of the alloy; otherwise the coating layer will be too thin.
3. The cleaning agent, slag-eliminating agent and gas-eliminating are suggested for floated slag treatment.
4. The solvent should be treated using special filter for solvent at regular intervals.
5. The baking temperature of the workpiece is suggested at 150℃~200℃ or antiknock is used.